À la journée du flash 2023, nous avons eu le plaisir d'accueillir Urs Tillmanns du magazine suisse spécialisé dans la photographie "Fotointern". Un article sur cette visite est publié sur https://www.fotointern.ch/arch... (uniquement en allemand). Avec l'aimable autorisation du magazine, nous publions également cet article sur notre blog:
"Les flashes Broncolor sont bien connus dans le milieu professionnel, et l'on sait aussi que les flashes et les accessoires sont fabriqués en Suisse, à Allschwil, près de Bâle. Fotointern a récemment eu l'occasion de visiter l'entreprise et de se faire une idée des processus de production passionnants.
L'histoire de Bron remonte à environ 75 ans, lorsque les frères Pierre et Joseph Bron ont fondé en 1948 la société Bron & Co à Bâle, dans laquelle ils enduisaient des lentilles et commercialisaient des appareils de radiographie et des accessoires photographiques. Un an plus tard, Dimitiri Rebikoff cherchait un distributeur pour ses flashs et trouva en les frères Bron un partenaire valable. Rebikoff arrêta sa production en 1952 et légua à la société Bron la licence de fabrication des flashes sous le nom de Broncolor.
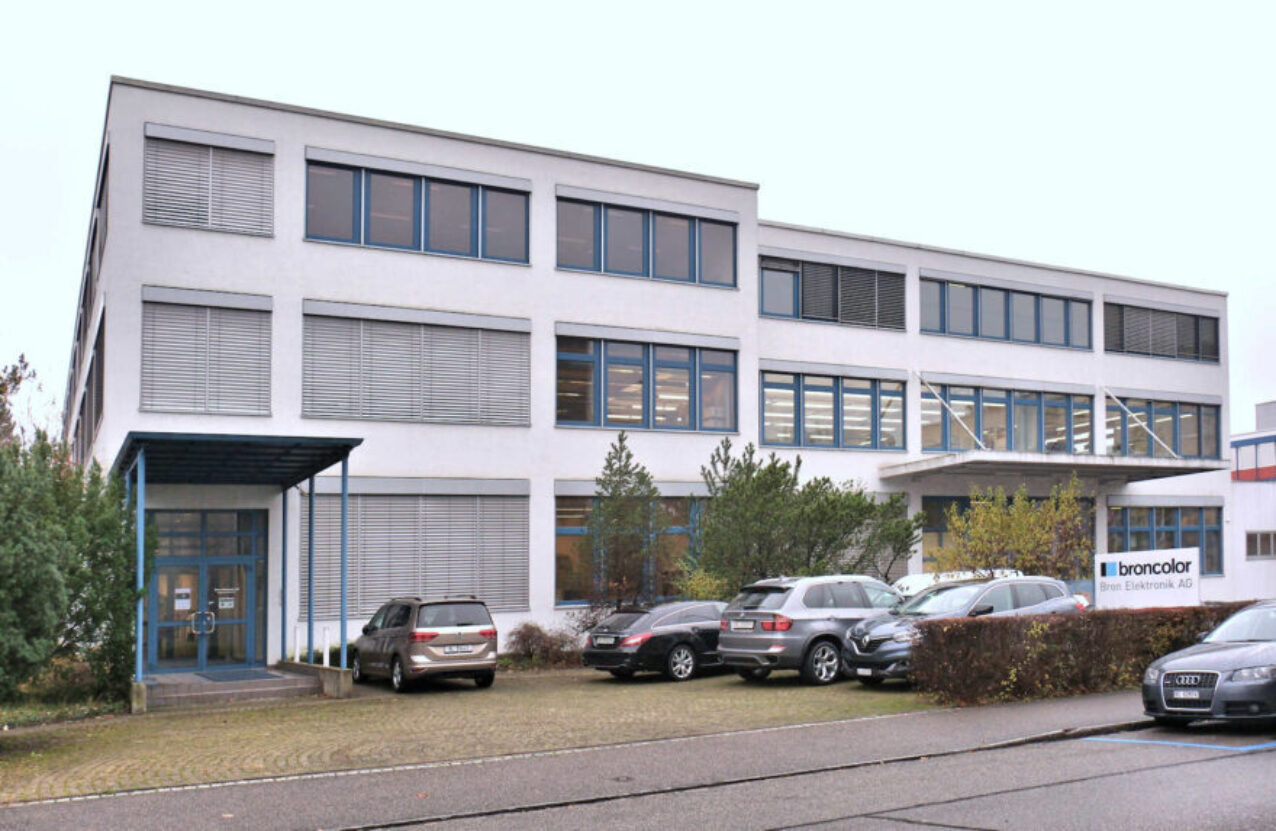
Le domicile de l'entreprise Bron Elektronik AG à Allschwil. Ici, tout est sous le même toit, du développement à la production en passant par l'expédition dans le monde entier.
Une longue histoire brièvement racontée. Depuis, la société Bron Elektronik AG a développé elle-même un grand nombre de générations d'appareils et les a fabriqués dans sa propre entreprise à Allschwil. Avec une petite équipe de développement, Bron a constamment appliqué les dernières technologies à ses appareils et, en tant qu'entreprise flexible, elle est en mesure de proposer des appareils de pointe qui aident les photographes professionnels à accomplir leurs tâches exigeantes avec un maximum d'efficacité et de confort de travail.
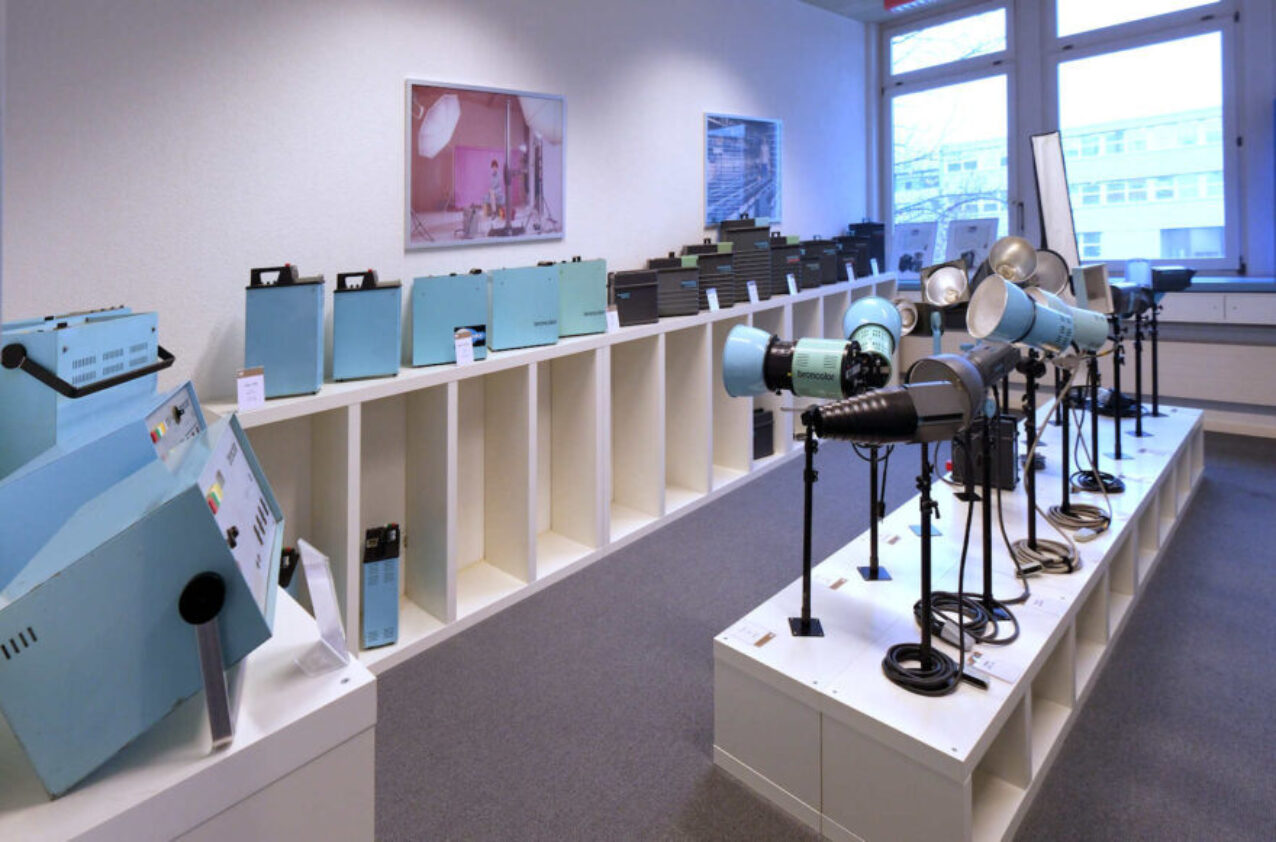
L'entreprise est légitimement fière de son histoire et c'est pourquoi elle conserve également les appareils devenus rares dans un petit musée.
Un coup d'œil dans les coulisses
Le bâtiment de l'entreprise Bron, Hagmattstrasse 7 à Allschwil, à un jet de pierre de la frontière française, abrite le développement, la production, le stockage et l'administration. Avec une cinquantaine d'employés, il s'agit d'une PME de taille moyenne, dans laquelle une quinzaine de personnes s'occupent de l'administration et de la logistique et environ 35 du développement, de la fabrication de sous-ensembles, du montage, de l'assurance qualité ainsi que de la gestion des stocks et de l'expédition. Une petite équipe donc, avec des processus de production clairs et efficaces.
La profondeur de fabrication des produits est étonnante. "Nous produisons autant que possible en interne et ne faisons fabriquer que des pièces spéciales en fonte d'aluminium, des pièces estampées, des pièces en plastique moulées par injection, des éléments optiques et quelques composants électroniques par des sous-traitants", explique le directeur de l'entreprise Daniel Niederhauser. Cela permet non seulement une fabrication flexible et des produits qui peuvent être rapidement adaptés aux tendances du marché et aux souhaits des clients, mais aussi une moindre dépendance vis-à-vis des sous-traitants.
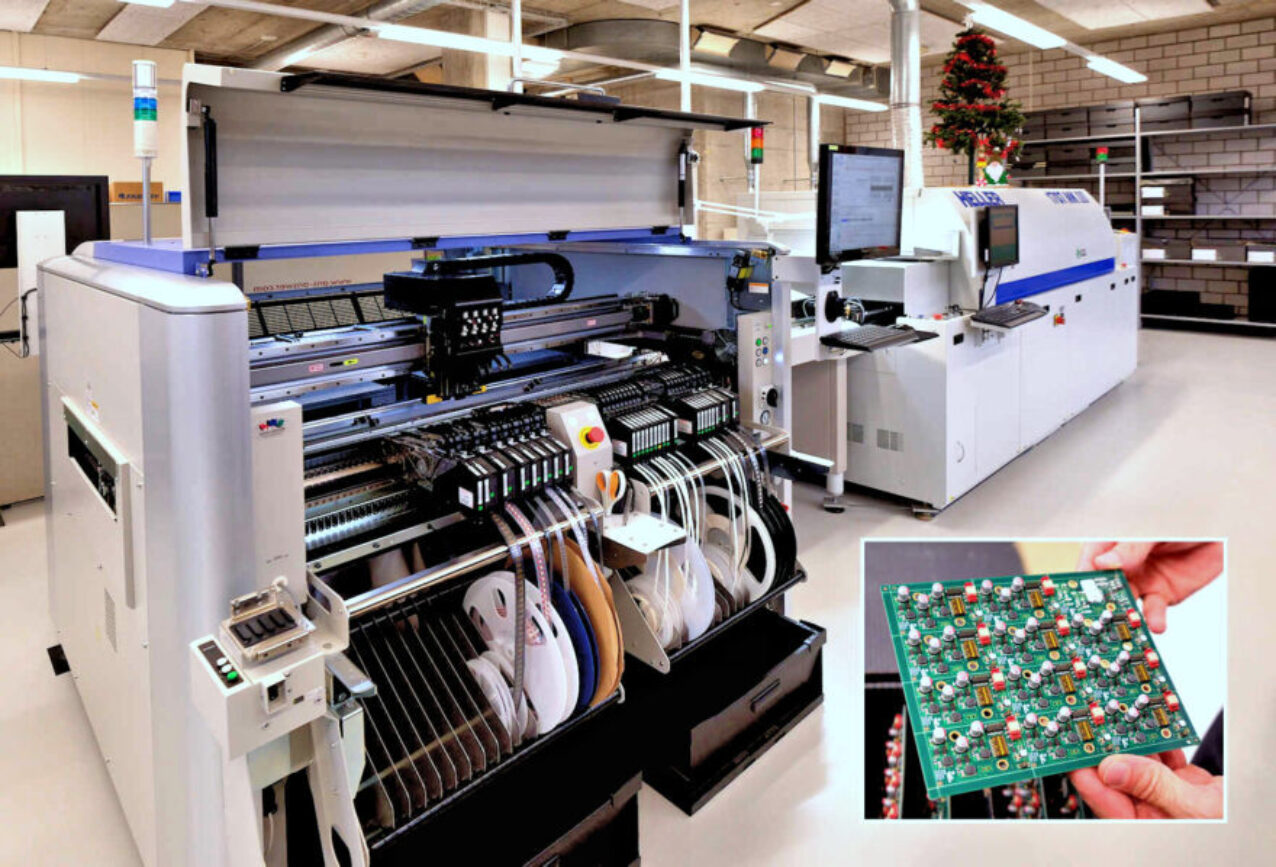
Un exemple en est la fabrication de circuits imprimés avec un automate de placement qui place les composants électroniques sur les platines à une vitesse époustouflante, au millième près, et qui les amène en ligne au tunnel de soudure. L'installation traite jusqu'à 64'000 composants de puces par heure ; le nombre de circuits imprimés finis dépend de la taille des platines à équiper et de la densité d'équipement.
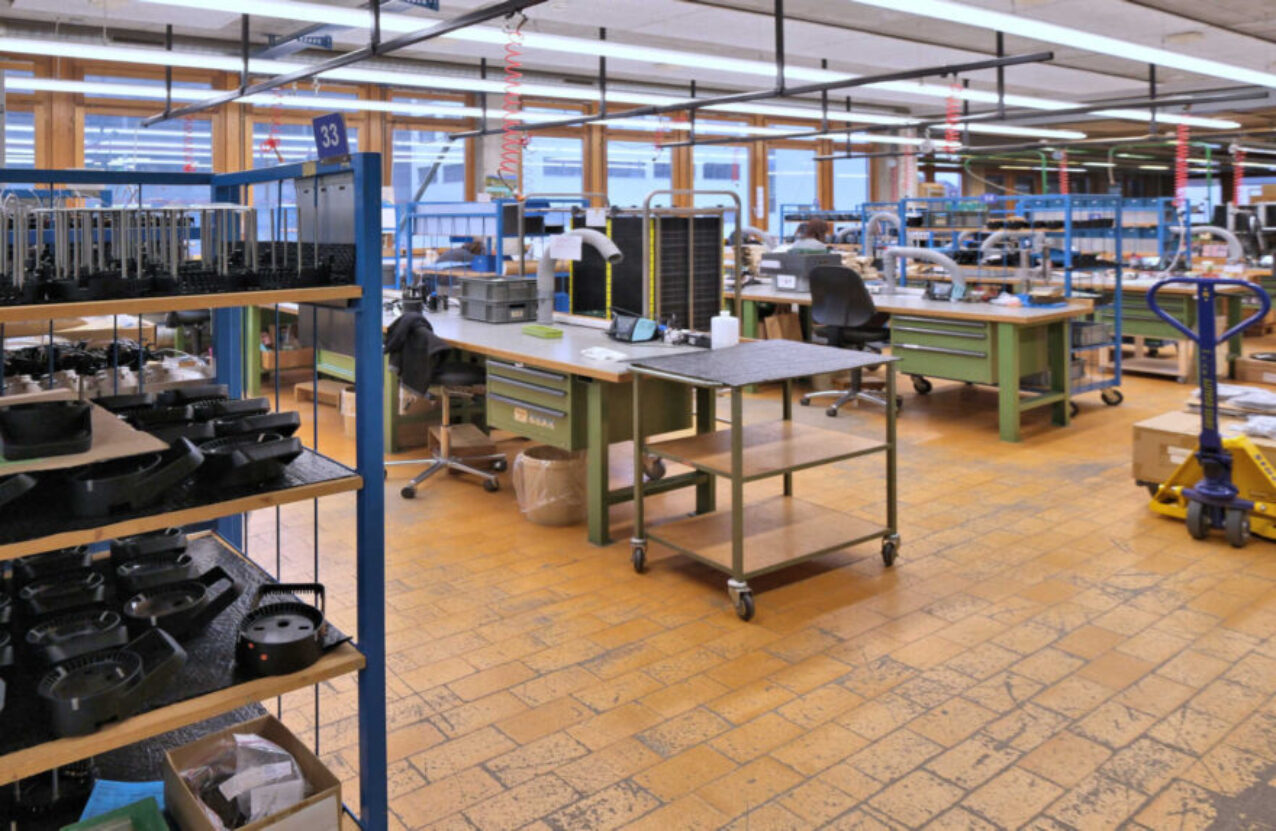
Vue de l'atelier de montage. Ici, les modules sont montés lot par lot sur des postes de travail individuels jusqu'aux appareils finis.
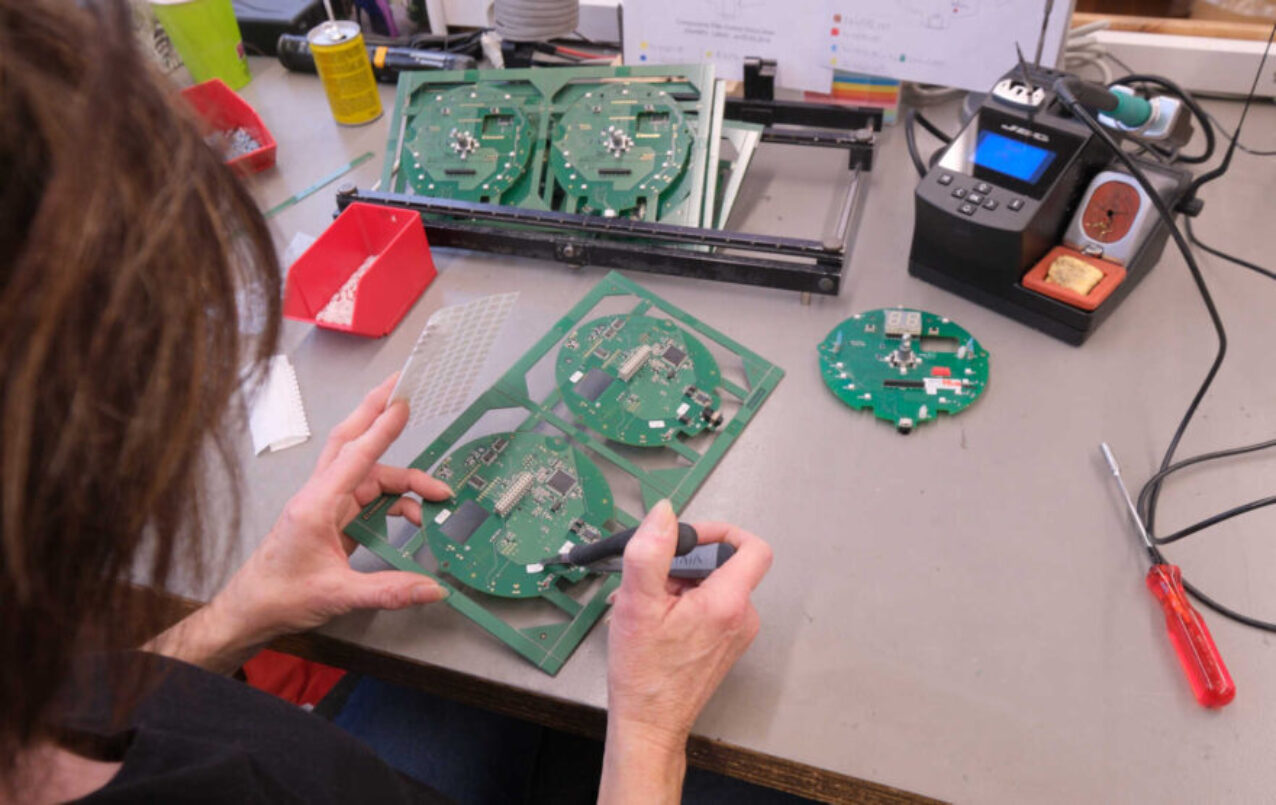
Ici, on reconnaît déjà la platine principale ronde d'un flash compact Siros. Après chaque étape de travail importante, un contrôle de qualité est effectué. De cette manière, le taux de défaillance est maintenu aussi bas que possible.
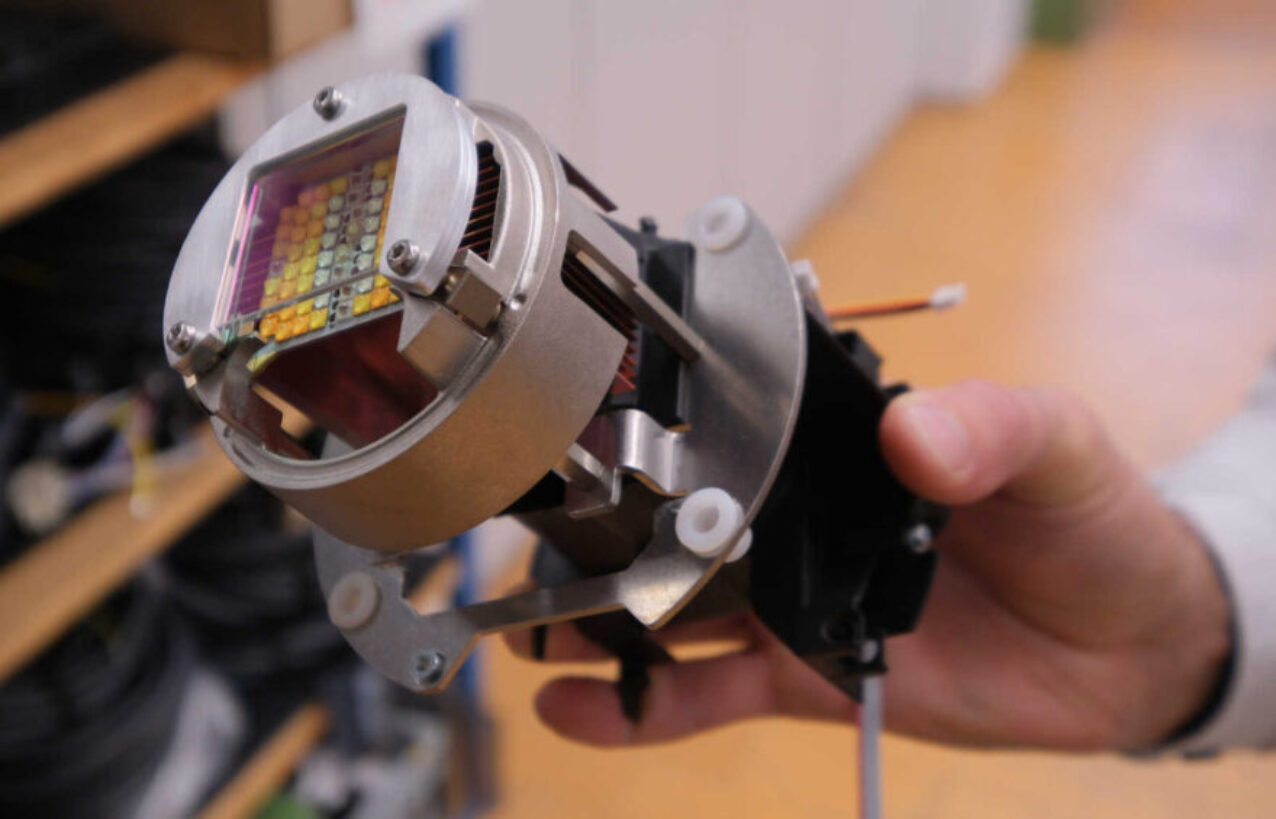
Voici l'intérieur d'une tête de torche. La lumière de mise au point est composée de nombreux éléments LED différents. Un filtre de protection thermique est placé devant.
"On parle toujours de lumière froide avec les LED. Ce n'est pas tout à fait vrai, car la chaleur est générée derrière les éléments et doit y être évacuée", explique Daniel Niederhauser. La lumière de mise au point revêt une importance croissante car, conformément à la tendance actuelle, les appareils sont souvent utilisés comme source de lumière continue pour les productions vidéo.
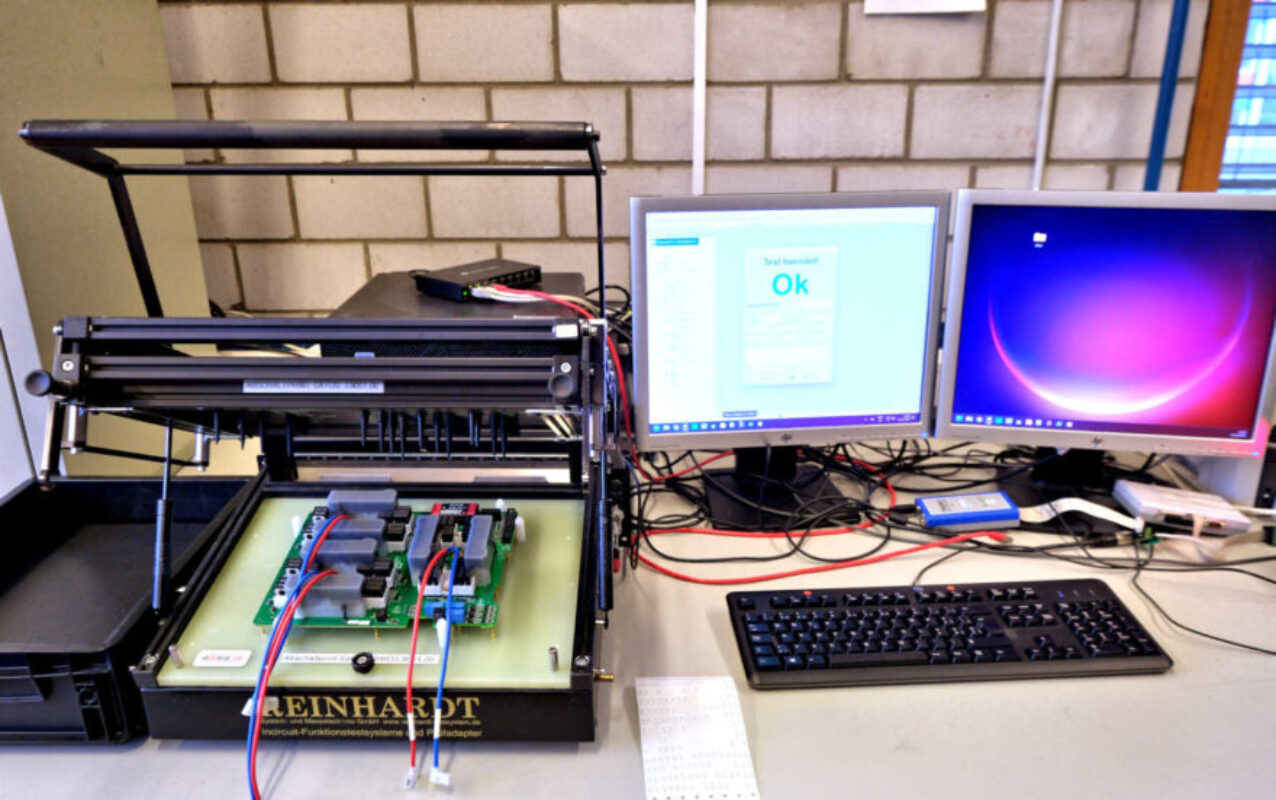
Dans cet adaptateur de test, les circuits électroniques sont soumis à un test in-circuit et fonctionnel, ou les prototypes peuvent également être programmés ici.
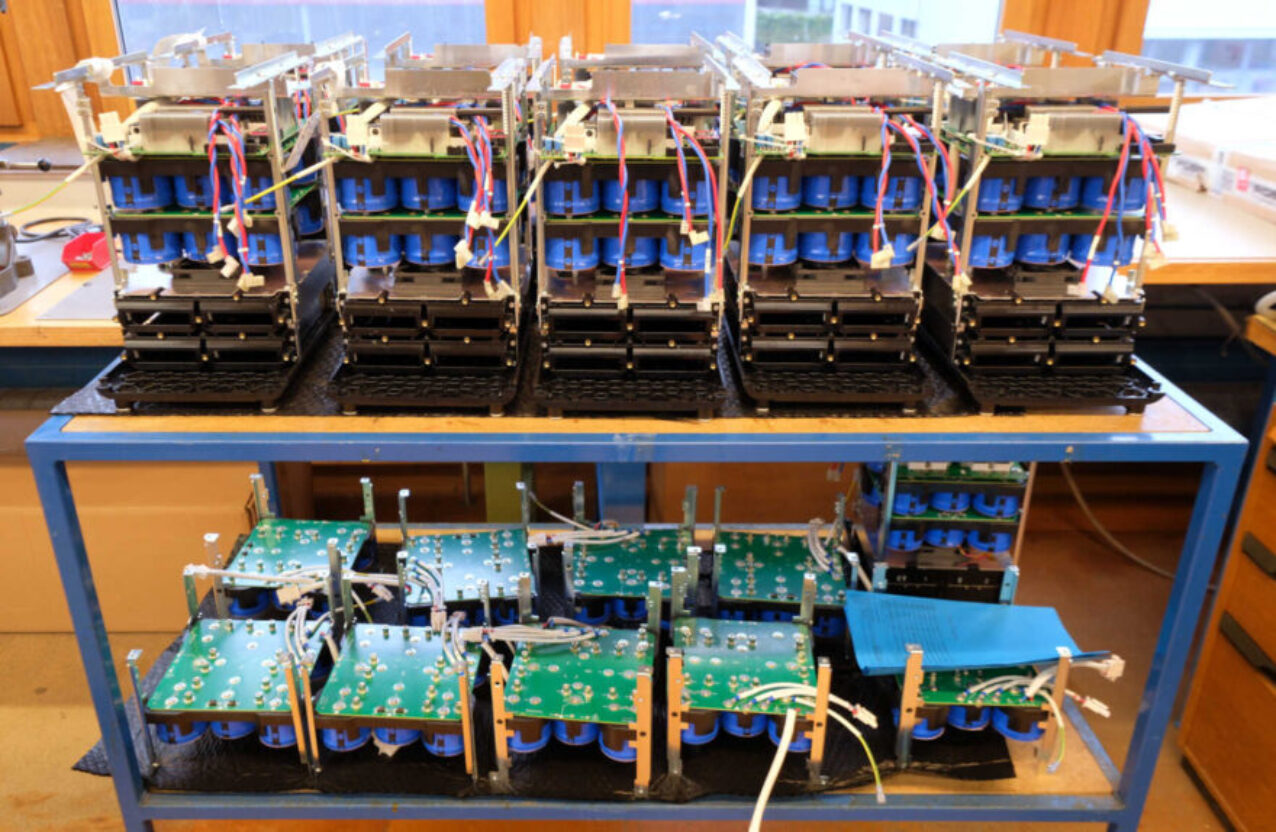
Les générateurs Satos entièrement montés attendent d'être installés dans les boîtiers. Ces derniers sont devenus de plus en plus compacts au cours des dernières décennies grâce à la miniaturisation des composants. "Il y a toutefois une limite à cela : Les condensateurs performants ne peuvent guère être construits plus petits. La puissance élevée nécessite justement de la place", explique Niederhauser.
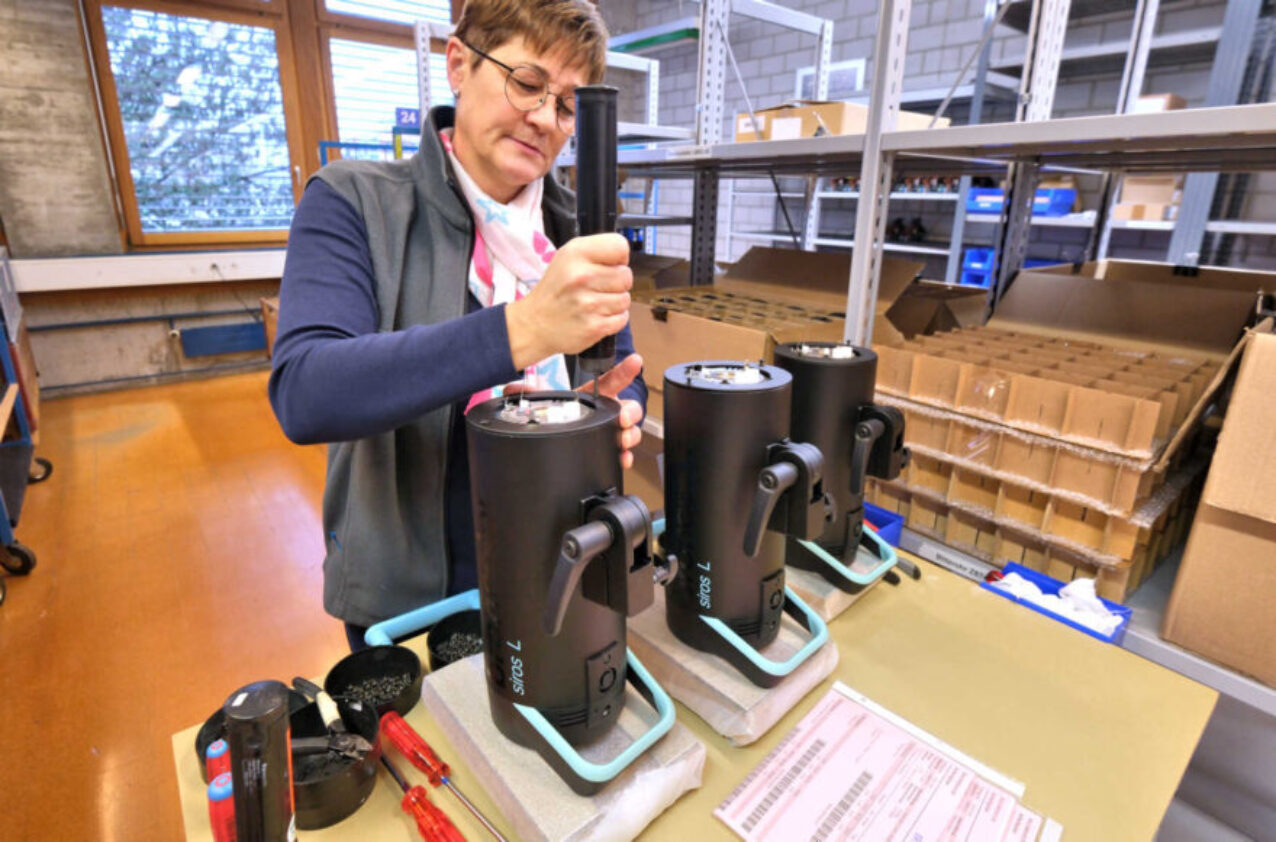
Montage final des flashes compacts Siros L. Ceux-ci sont de plus en plus appréciés des photographes professionnels en raison de leur puissance élevée et de leur vaste système d'accessoires - en particulier pour les missions en extérieur.
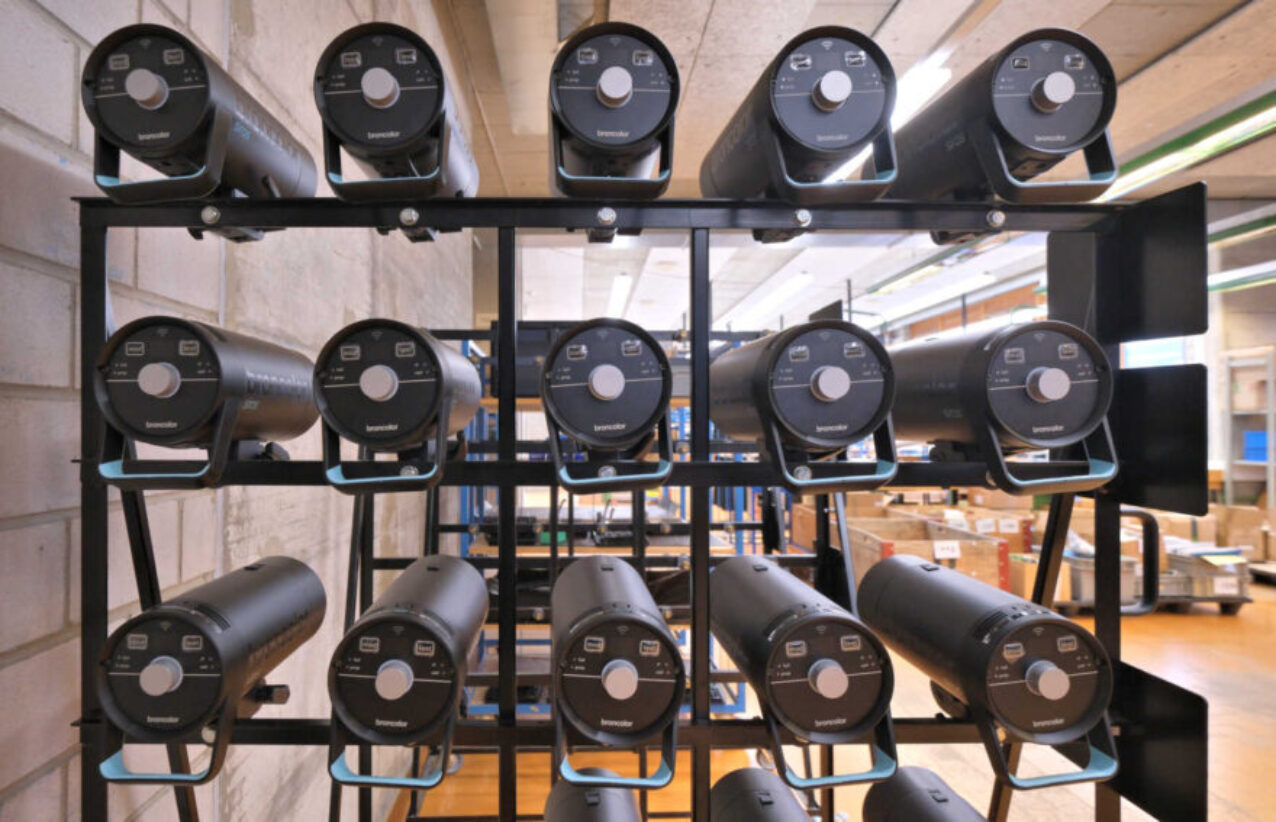
Une fois assemblés, les flashes compacts Siros attendent leur firmware, le contrôle qualité et le test de résistance. Ce n'est qu'ensuite qu'ils entament leur voyage vers leurs futurs prestataires de services.
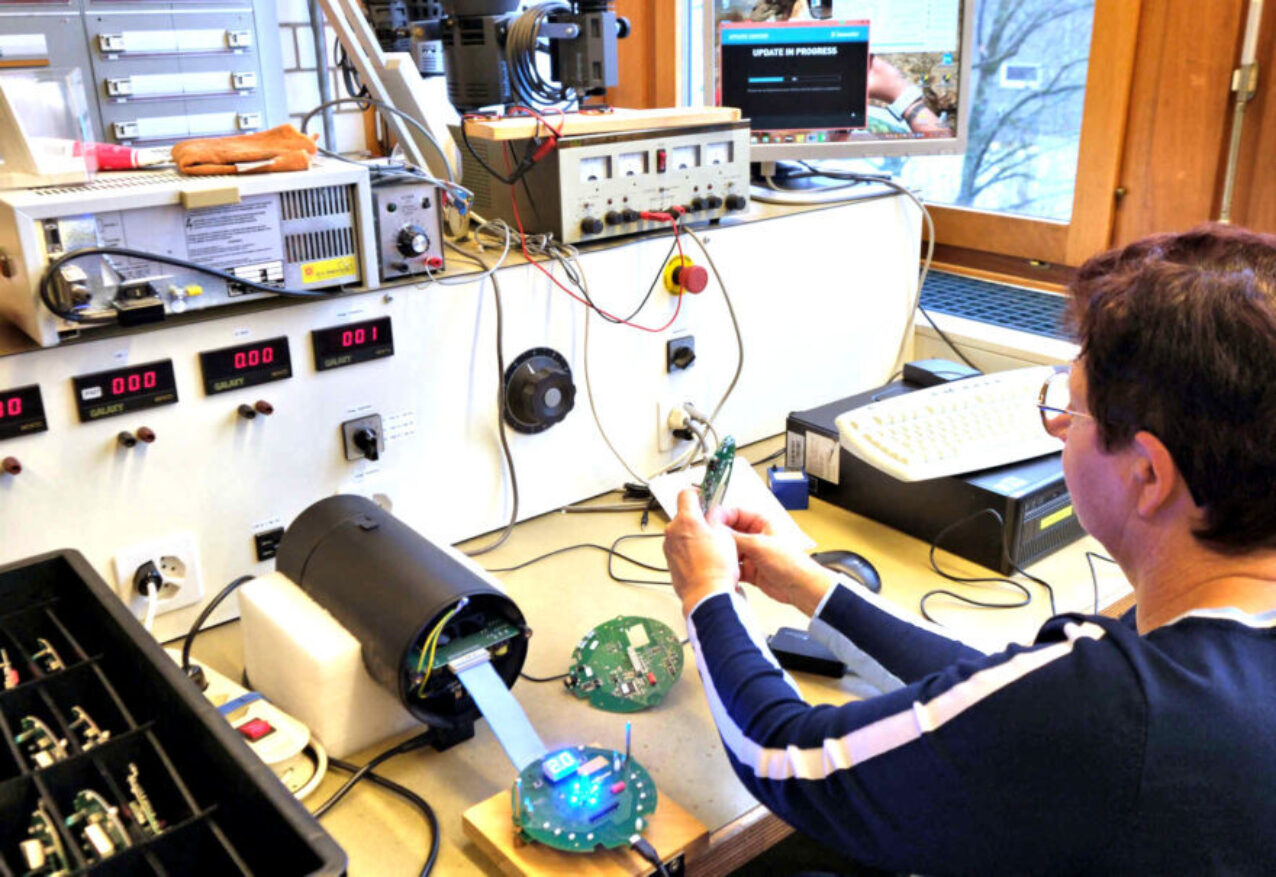
Là, les flashes sont soumis à un contrôle final très strict.
Tout est mesuré, calibré et les données sont enregistrées. Enfin, le logiciel est installé. Lors du développement de ce dernier, qui se fait également en interne, on veille à ce que les nouvelles caractéristiques et fonctions puissent également être utilisées sur les appareils plus anciens grâce aux mises à jour correspondantes du micrologiciel.
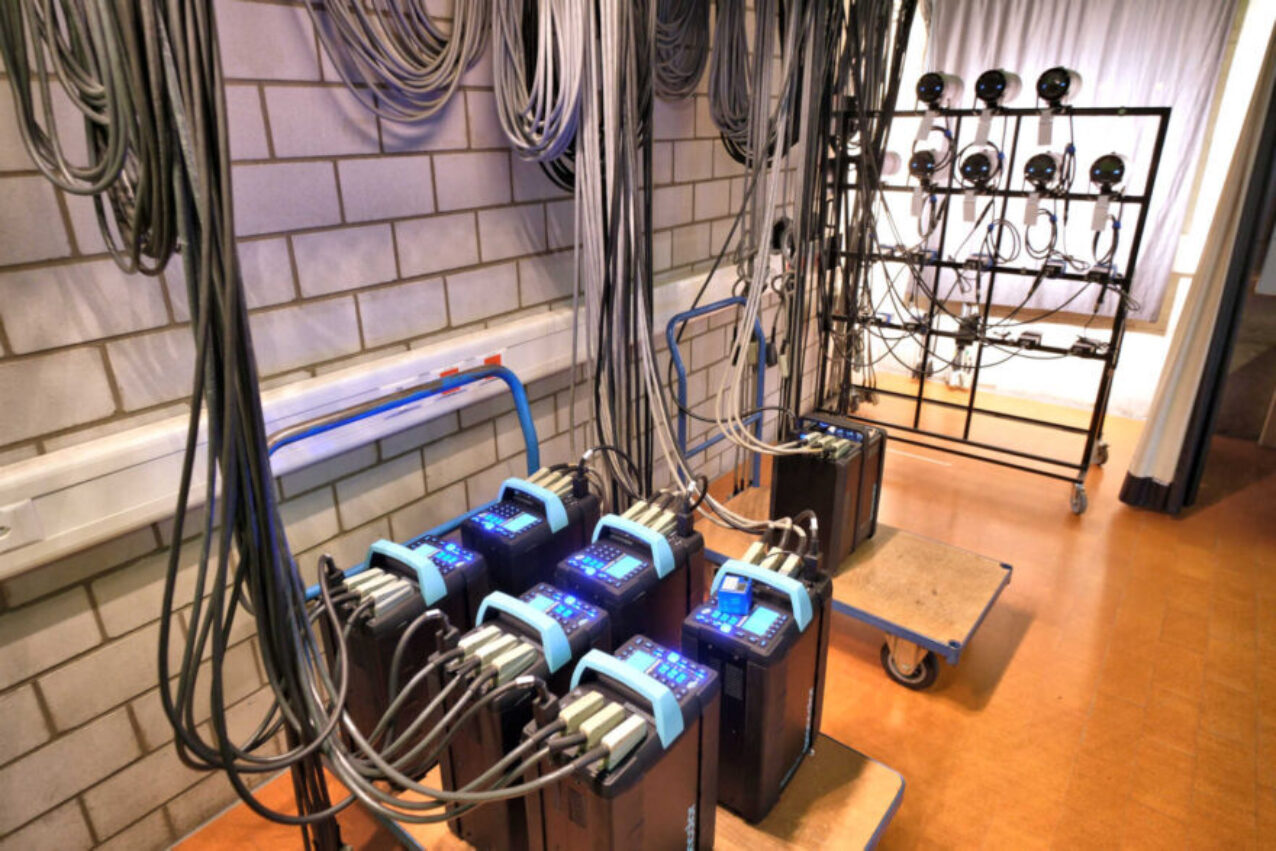
Ensuite, c'est le départ pour la salle de torture. Ici, chaque appareil est soumis à un test d'endurance avec plus de mille éclairs - une véritable tempête d'éclairs. Après ce "burn-in test", chaque appareil subit un nouveau passage de contrôle. Chaque détail est consigné avec précision pour chaque appareil afin de pouvoir déterminer la cause éventuelle en cas de réparation ou de réclamation.
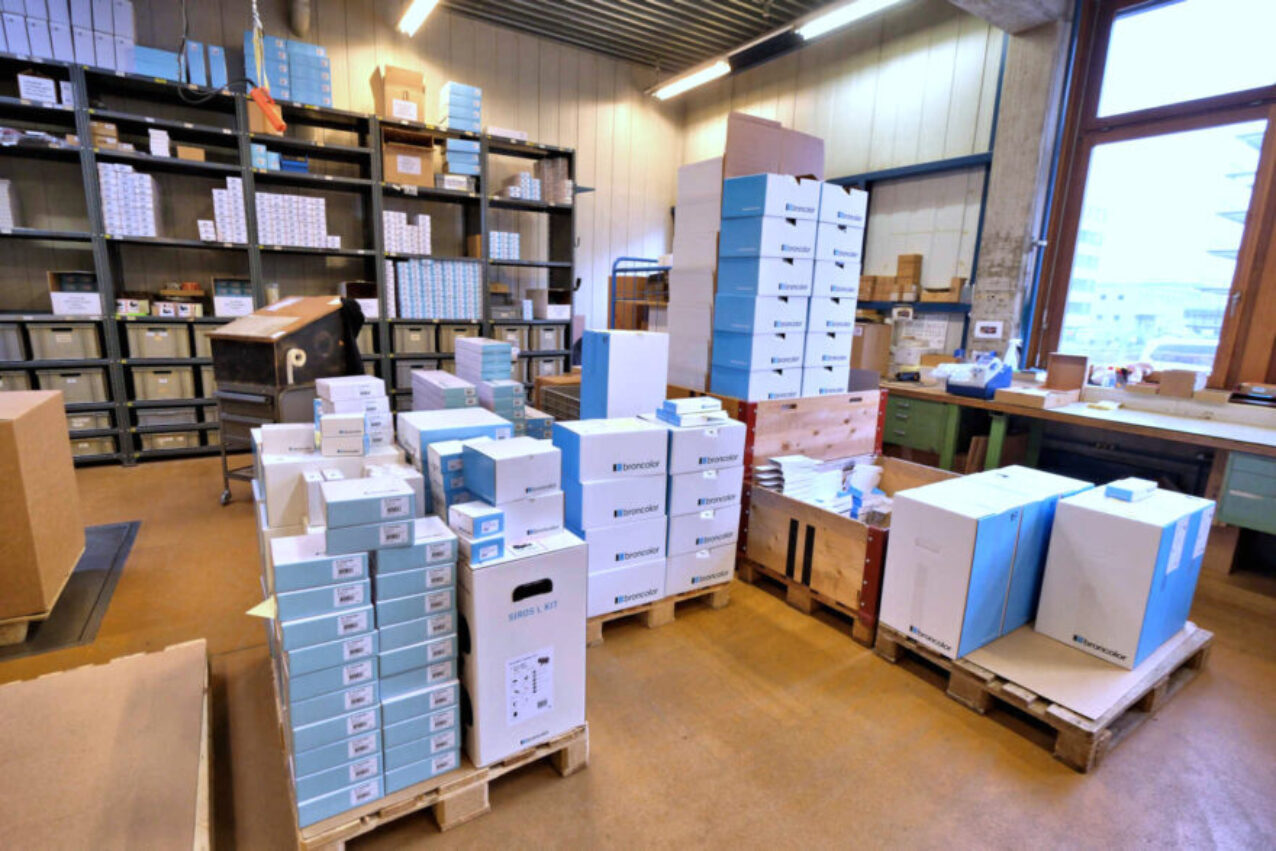
Vue de l'entreprise de transport. C'est ici que les produits finis sont préparés pour leur voyage et ensuite envoyés dans plus de 60 pays. En fonction de la destination, l'expédition se fait sous douane, ce qui permet une livraison particulièrement fluide et rapide.
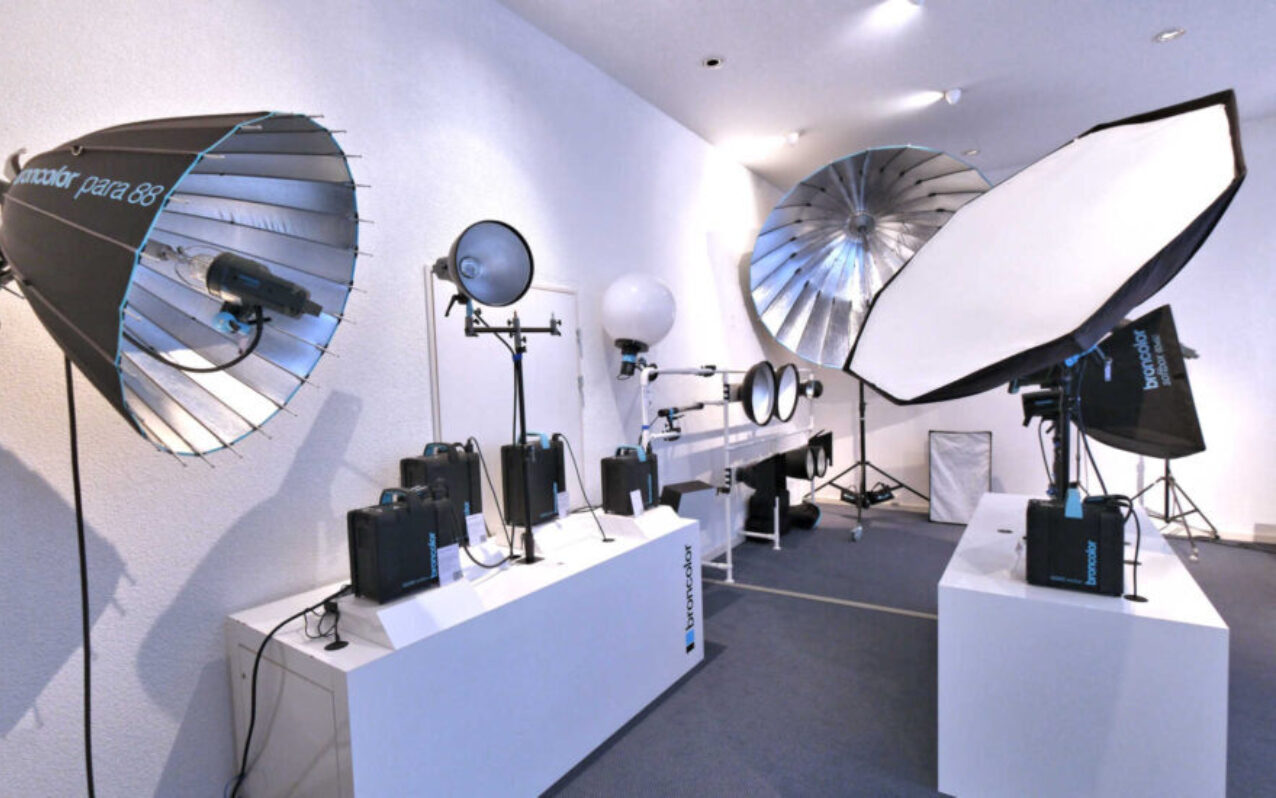
Bron Elektronik AG dispose également d'un showroom où sont exposés tous les produits actuels. Ce showroom est moins destiné aux consommateurs finaux qu'aux clients commerciaux qui distribuent les appareils Broncolor dans leur pays.
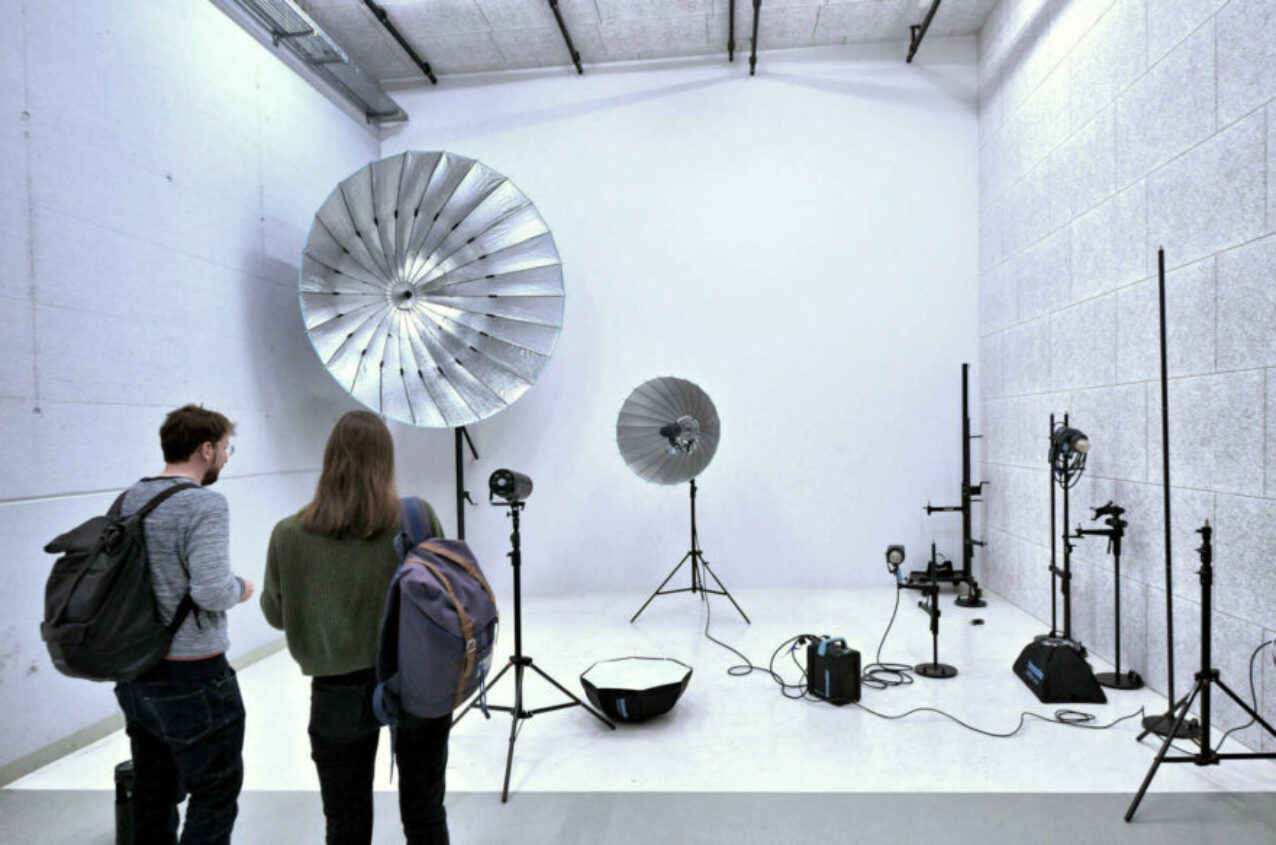
Bron dispose également d'un imposant studio photo où les nouveaux appareils et modeleurs de lumière sont testés dans la pratique, mais où des ateliers et des cours sont également organisés.
Conclusion
Au terme d'une journée intéressante, nous avons eu un aperçu captivant d'une usine dont on se souvient surtout pour son taux élevé de fabrication interne et son contrôle qualité impressionnant. Cette qualité et le "Made in Switzerland" ont aussi leur prix. Les appareils Broncolor ne sont pas bon marché, mais ils garantissent la durabilité et la fiabilité - des facteurs importants dans le travail exigeant de la photographie professionnelle."
Texte et images:
Urs Tillmanns / Fotointern.ch
Article original: